Suzhou plastic water tank manufacturer
The method to deal with bubbles in plastic bucket production is to increase injection energy, pressure, speed, time and material amount, and increase back pressure to make the mold full. Increase material temperature and flow smoothly. Reduce the material temperature and shrinkage, and advance the mold temperature properly, especially the part of mold temperature that constitutes the vacuum bubble. The gate is set at the thick part of the workpiece to improve the activity of the nozzle, runner and gate and reduce the consumption of pressing. Improve the mold exhaust condition. The uneven movement of plastic in the mold makes the air trapped in it. When the plastic enters the warm air workshop, the moisture will condense on the cold plastic. The recommended remedy is to dry the plastic. Store the polymer in the workshop for at least six hours before injection molding. The plastic bucket is used to store all kinds of liquids. When we install the liquid and screw the vent cover, we need to lie on the side for one minute first, so that the vent film can be stored vertically after soaking the liquid. The storage temperature of the plastic bucket should also be noted, which is generally about 40~50 ℃. After a certain period of storage, check whether there is expansion. If the bulge is serious, it means that the ventilation cap is not applicable

Suzhou plastic water tank manufacturer
When the surface of the plastic bucket is labeled, the labeling surface should be flat. A "frame" can be designed on the surface of the plastic bottle, so that the label can be positioned accurately without movement. During blow molding, the first contact part of parison inflation always tends to be the first hardened part. Therefore, the wall thickness of this part is also larger. The edge and corner are the parts where parison inflation contacts, and the wall thickness of this part is small. Therefore, the edges and corners of plastic bottles should be designed as rounded corners. The rigidity and bending resistance of plastic bottles can be improved by changing the surface shape of the plastic bottle, such as making the middle of the plastic bottle relatively thin, and increasing the circumferential grooves or ribs on the surface of the plastic bottle. The longitudinal grooves or stiffeners can eliminate the deviation, sagging or deformation of plastic bottles under long-term load. The printing surface of the plastic bucket is where consumers focus their attention. The printing surface shall be flat and continuous; If the plastic bottle contains a handle, a groove, a reinforcing rib and other structures, attention should be paid not to inconvenience the printing operation during the design. The elliptical plastic bottle has high rigidity, but the manufacturing cost of the mold is high. Therefore, in order to ensure the rigidity of the plastic bottle, in addition to selecting materials with high rigidity, it is also necessary to enhance the rigidity and load resistance strength of the plastic bottle through the shape design of the plastic bottle.

Suzhou plastic water tank manufacturer
Plastic barrel modification equipment What are the processing equipment for plastics? Plastic barrel modification equipment Plastic modification involves four aspects: raw and auxiliary materials used, processing equipment, modification technology and effect, and specific application. According to the plastic modification process, the processing equipment can generally be divided into four categories: primary mixing, melt mixing, pelletizing and drying. The corresponding equipment is introduced as follows: primary mixing equipment. Primary mixing equipment refers to the equipment used for mixing materials in the non melting state. The equipment used for primary mixing is almost intermittent. There are many types of primary mixing equipment, such as rotary drum mixer, double cone mixer, spiral belt mixer, Z-shaped kneader high-speed mixer, etc., but at present, the two types of widely used plastic mixing processes are Z-shaped kneader and high-speed mixer. Z-shaped kneader Z-shaped kneader, also called double arm kneader, is mainly composed of rotor, mixing chamber and driving device. The rotor is installed in the mixing chamber. The mixing chamber is a steel trough with a W-shaped or saddle shaped bottom. The upper part is provided with a cover and a feeding port, and the lower part is generally provided with a discharge port. The steel trough is jacket type, and heating and cooling medium can be fed into it. Some high-precision mixing chambers are also equipped with vacuum devices, which can discharge moisture and volatile matter during the mixing process. There are two types of rotor installation in the mixing chamber, one is tangential installation and the other is intersecting installation. In tangential installation, the movement traces of the outer edges of the two rotors are tangent; In the intersecting installation, the movement traces of the outer edges of the two rotors are intersecting. During tangential installation, the rotor can rotate in the same direction or in different directions, and the speed ratio between rotors is 1.5:1, 2:1 or 3:1. The rotor installed in intersecting mode can only rotate at the same speed because the outer edge movement traces intersect. The clearance between the outer edge of the rotor installed in an intersecting manner and the wall of the mixing chamber is very small, generally about 1mm. In such a small gap, materials will be strongly sheared and squeezed. This effect can be physically modified by filling and blending.

Suzhou plastic water tank manufacturer
What factors will affect the performance of the plastic bucket? At present, plastic buckets are common to us, and everyone will use them. The performance of plastic bucket is very advantageous. You can choose different plastic buckets according to different liquids. The production process of the seemingly simple plastic bucket is not so simple. When producing plastic buckets, the manufacturers of plastic buckets still need to pay attention to some small problems that will affect the performance of the finished plastic buckets, which will greatly reduce the sales rate of plastic buckets. 1. The blowing speed determines the performance of plastic bucket products. 2. The cold temperature time determines the performance of plastic bucket products. 3. The expansion rate determines the performance of plastic bucket products. 4. Uneven longitudinal wall thickness of plastic bucket products determines the performance of products. 5. The performance of plastic bucket products is determined by the uneven horizontal wall thickness. 6. Plasticizing temperature and time determine the performance of plastic bucket products.

Suzhou plastic water tank manufacturer
How to deal with the liquid container after use? The used liquid packaging barrels are not allowed to be thrown randomly, and must be disposed properly, otherwise it will cause environmental pollution. Pay attention to the following points when handling: 1. First, ensure that the vehicles transporting liquid packaging barrels are in good condition. 2. Construction waste: waste oil drums, waste paint drums, waste fire extinguisher cans, waste plastic cloth, waste chemical materials and their packaging materials, waste glass fiber cloth, etc., shall be disposed according to relevant regulations, and shall not be discharged at will, otherwise serious harm will be caused. 3. Try to recycle the waste and do not cause secondary pollution. According to the requirements of relevant national laws and regulations, the waste paint bucket in the liquid packaging bucket belongs to hazardous waste. Recycling can only be done by a qualified waste disposal company. However, there are a large number of waste paint buckets, each of which is 1.5kg-2k. If hazardous waste is treated, a lot of treatment costs will be incurred.
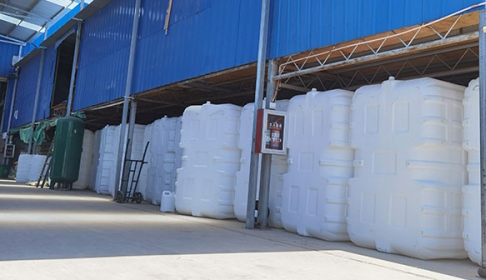
Suzhou plastic water tank manufacturer
There are several ways to remove the residue on the plastic packaging bucket: because the plastic packaging bucket is made of PE, after using the plastic bucket, there will be a lot of oil stains on the inner wall of the bucket, and it is also very difficult and troublesome to clean. Now, Shandong Zhongcheng Packaging Co., Ltd. will introduce the method to remove the residue of plastic chemical barrels. When we remove the residue on the chemical barrel, whether using polishing water or vinegar, we should ensure that it is soaked for a long time, so as to ensure that the residue in the barrel can be removed. Find a piece of dry cloth dipped with vinegar to cover it on the chemical plastic bucket with residue. After the impurities on the bucket are soaked, use a hard small slice to easily remove the residue of trade.