Plastic water storage tank The common shrinkage problem has been puzzling everyone, as follows Shaanxi Faxiang Plastic Co., Ltd Let's introduce the solution.
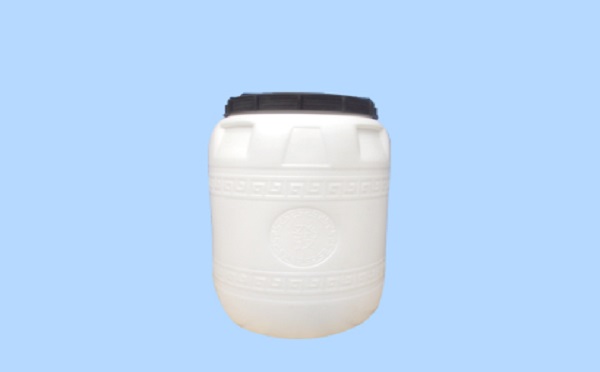
Xi'an plastic bucket manufacturer Let me tell you that there are four cases of plastic shrinkage:
Thermal shrinkage, phase transformation shrinkage, orientation shrinkage, compression shrinkage and elastic recovery. The shrinkage process consists of shrinkage before solidification, cooling shrinkage and shrinkage after demoulding.
Main reasons for shrinkage:
1. Insufficient injection volume; 2. The melt temperature is too high; 3. The injection pressure and pressure maintaining pressure are too small; 4. Too little injection time and pressure holding time; 5. The injection speed is too fast; 6. The mold temperature is inappropriate.
Main reasons for shrinkage:
1. Insufficient injection volume; 2. The injection pressure is too low; 3. Improper injection speed; 4. The mold temperature is too low.
1. Injection molded parts lack glue and do not fill the mold
Cause analysis: the cavity is not completely filled with plastic melt. The fluidity of plastic materials is poor.
Countermeasures: If the product is improperly matched with the injection molding machine, and the plasticizing capacity or injection volume of the injection molding machine is insufficient, the appropriate injection molding machine should be selected. Insufficient melting and poor fluidity of plastics lead to large injection pressure loss. Increase the number of gates, reasonably arrange the gate position, and uneven layout and filling of the perforated holes.
2、 φ Peak value (burr)
Cause analysis: The plastic melt will flow into the parting surface or insert mating surface. The mold locking force is sufficient, but a layer of redundant rubber film will be generated at the junction of the main gate and the separator.
Countermeasures: Insufficient clamping force. The high-pressure plastic injected into the cavity forms a gap on the parting surface or mating surface of the insert, and the plastic melt overflows into the gap. The die (fixed side) does not fully contact the machine nozzle, resulting in a gap between the male and female dies. The influence of mold temperature on crankshaft clamping system. Improve the strength and parallelism of the formwork. Die guide post sleeve is worn/die mounting plate is damaged/pull rod (core column) is bent due to insufficient strength, resulting in deviation of parting surface. Foreign matters adhere to the parting surface. The exhaust slot is too deep. The projection surface of the cavity is too large/the plastic temperature is too high/the pressure is too high
3. Surface shrinkage and shrinkage cavity (vacuum bubble)
Shaanxi plastic bucket manufacturer Cause analysis: the product surface is concave. This is caused by plastic volume shrinkage, which is common in locally thicker areas, such as the connection area between the stiffener or column location and the surface. The vacuum bubbles generated due to the volume contraction of the local meat thickness of the product during the cooling process are called voids. When the plastic melt contains air, water and volatile gas, the residual cavity formed when air, water and volatile gas enter the product during injection molding is called bubble.
Countermeasures: increase the size of gate and runner, so that the pressure can effectively act on the thick plate of molded products. If necessary, the position of the rubber port can also be adjusted. Increase the holding pressure and extend the holding time. By increasing the filling speed, the plastic can be fully compressed before cooling and curing. Glue injection is transferred to pressure maintaining too fast. The thickness of the meat changes more smoothly, and the cooling efficiency of this part is improved. The colloidal particles are completely dried in advance to remove water. The cylinder temperature should not be set too high, which can effectively prevent the generation of plastic decomposition gas. Replace small screws or machines to prevent excessive shearing of screws. Increase the back pressure so that the gas can be discharged from the barrel. Properly reduce the filling speed and allow enough time to discharge the gas.
4. Cracking (material and water)
Plastic bucket manufacturer Cause analysis: there are silver white stripes on or near the product surface along the plastic flow direction. The production of silver wire is usually caused by the gasification of plastic attached to the mold surface or water or volatile substances in water. Sometimes, when the screw of the injection molding machine is involved in the air, silver bars will also be produced. This material has impurities.
Countermeasures: Rubber particles shall be fully dried in advance to remove moisture. The plastic melt decomposes due to overheating or staying in the barrel for a long time, producing a large amount of gas. The gas should be completely discharged to avoid silver wire. The mold temperature must reach the set temperature to avoid incomplete exhaust caused by rapid solidification of plastic melt.